PyCAE engineering services
Structural calculation
Structural calculation models the mechanical behavior of an assembly or isolated part, in order to predict and correct the unwilling behaviors : rupture, permanent deformation after loading, loss of stiffness (buckling), low lifetime (cyclic loading induces Fatigue theory), destructive resonance of a system, … It gives the possibility to optimize mass, stiffness, strength and lifetime (amongst others …) of a system. It gives the possibility to optimize mass, stiffness, strength and lifetime (amongst others …) of a system.
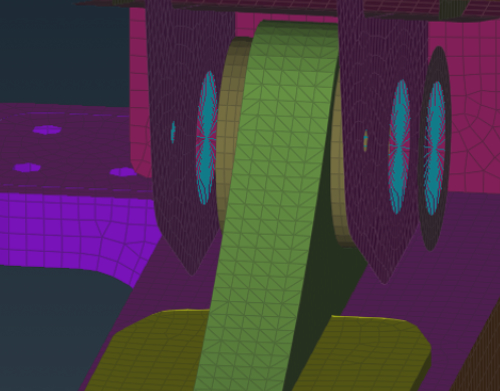
That consists in thinking about the physical problem and potentially realizing first analytical calculation (hypothesis) that could answer a first strength check of the system. Simplification have their own limits, so we very often creates a Finite Element model of the system, thanks to some specific software ; this numerical method stipulates that the overall behavior of the system is known, while each local element behavior is approximated:
- Discretization – meshing.
- Interfaces between parts modeling : contact, bolting, welding, …
- Loading applied to the system : bolting load, fretting, thermal loading, acceleration, local or distributed load (mass, pressure, …)
- Boundary conditions of the sytem : how the system is mounted in its own environment ?
All these info are written in an input ASCII file that a solver will read in (ABAQUS, NASTRAN, OPTISTRUCT, …); this solver will then write out responses of the system to the different loads and conditions; this results file is read via another software in order for the engineer to understand and analyze easily the system and give conclusion to the design team.
Fatigue calculation
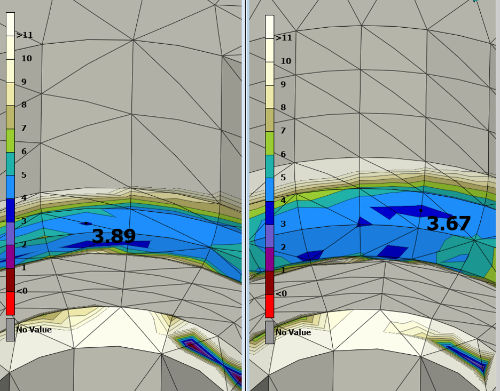
Analysis of a part failure under cyclic loading (recess in a engine cylinder-head with small radius).
Under cyclic loading, even below the elastic limit of the material, parts can suffer micro-crack, then crack propagation due to defect in the material, that will ultimately lead to rupture.
Fatigue study is effectively the analysis of the part cracking under cyclic loading, depending on defect quantity and/or sizes, stress distribution or local stress concentration, (thermal fieldnot evenly distributed, static bolting, dynamic loading, …), roughness, surface treatment inducing differents mechanical properties within the material …
Each material has its own behavior in regards to fatigue loading, depending on its composition but also material or surface treatment. Production method of the raw material and the part itself (surface roughness machined, grinded, casted, 3D printed...) will also induce potential residual stress that will influence the part lifetime.
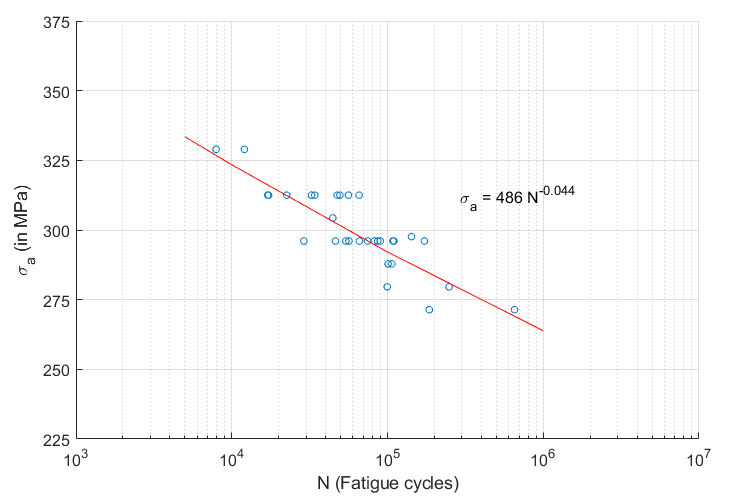
For a defined mean stress (not specified here), a stress amplitude of 300 MPa will lead to rupture after 55 000 loading cycles.
Topology optimisation
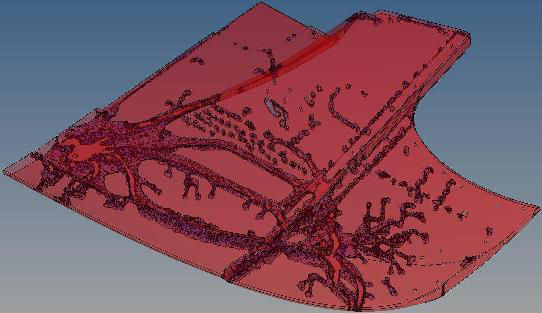
Example of a front wing (static loading from FIA homologation tests + aerodynamic pressure at full speed). The areas filled with material are showing the most efficient route to transfer loading according to all those loadcases, rest of the structure can be hollow.
Topology optimisation is coupling a optimisation loop with several loadcases : that needs defining targets (mass of the system, stiffness in a specific direction, maximum displacement allowed, minimum safety factor, …) the loop will try to achieve while modifying the shape of the system ; the results of the loop is a mesh that fits the targets defined.
In fact, we discretise the full volume, that could be defined fully or partially as ‘design space’ , and we apply loadings and boundary conditions to this complete mesh. The solver calculates the 1st iteration as defined and will get its first values to compare to the targets defined. Each iteration, the solver will try targetting the defined mass while changing the density of each element in the design space (element density equals to 0 means the element does not play any rôle in the load transfer). Each iteration, the solver will try targetting the defined mass while changing the density of each element in the design space (element density equals to 0 means the element does not play any rôle in the load transfer).